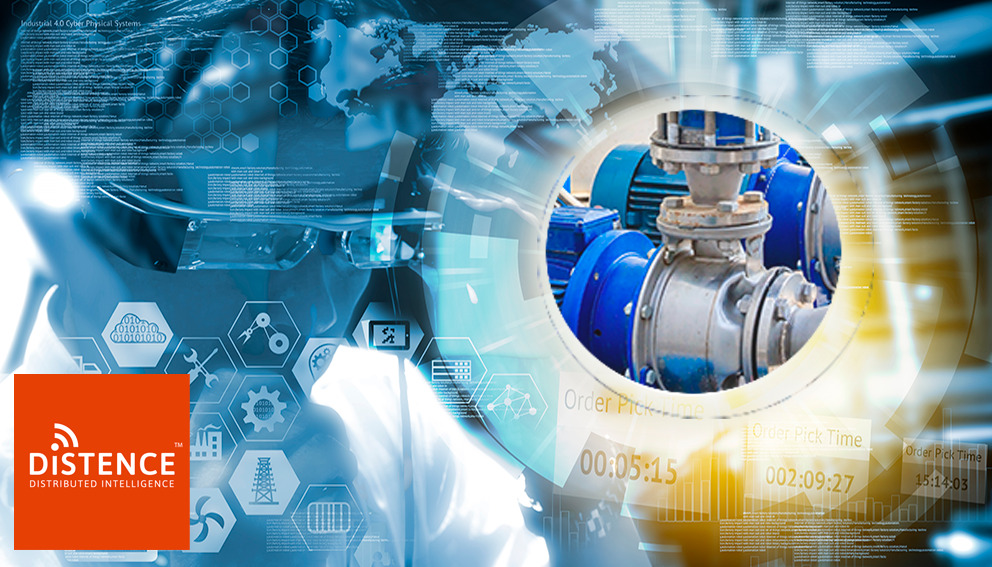
Many of us have moved to remote working from home office to support the fight against the COVID-19. This is usually possible in white-collar positions as the way of working can be adopted relatively easy to the prevailing situation. Remote collaboration tools are the new norm for many.
For those who work in areas where physical presence is required, the challenge is somewhat different. The COVID-19 has highlighted a new challenge – restricted movement or access of people. Even with the high growth rate of automation in industrial manufacturing, many tasks are still perceived as requiring on-site presence. One being condition monitoring of rotating machinery.
We at Distence developed our first concept of remote monitoring and analysis for wind turbines more than a decade ago. The operational requirements we face today were not so different then – “need to perform precision analysis on relevant data, e.g. vibrations, and to access close to real time raw measurement data anytime, anywhere, around the globe”.
“free knowhow intensive work from time and place…”
The objective was to scale the efficiency of highly skilled and scarce resources, e.g. a CAT IV vibration analyst, and free the knowhow intensive work from time and place. This journey has continued, and today the remote services model is more or less a standard in wind power industry. The top drivers for this development were the demand for reliability and cost efficiency of monitoring and repairs. The adoption of remote monitoring was accelerated as cost-efficient technology became available in the early days of the wind power industry.
With the adoption of a new on-line and virtual model, sharing the learnings from global scale remote condition monitoring can eliminate redundancy of maintenance teams on-site. In the condition monitoring of rotating machines, the old process is often dependent on professionals with knowhow and measurement tools travelling from site to site.
Plenty of tacit knowledge locked inside these teams and on the memory chips of their measurement hardware and laptops. Today, however, data acquisition and analysis can be automatized with solutions built on agile and cost-efficient architectures so that the skilled professionals can focus more on knowhow intensive tasks and less on sitting in service vans. Not to mention, all this with increased safety. Remote monitoring reduces radically the impact of sudden unforeseen factors, like sick leaves, pandemics or sudden shortage of manpower.
“Remote monitoring reduces radically
the impact of sudden unforeseen factors…”
Continuous analysis identifies budding issues, failing components and buys the crew time to act with a plan. Information and analysis can be shared without delay with, for example, an external service provider. With remote and automatized condition monitoring, responsibilities can be shared and evened out.
Up until now, monitoring systems have been built on old existing systems, collecting limited data from e.g. PLC’s or they have been built as dedicated point-to-point systems. Often the systems have been built over time with components from several suppliers, resulting in a large number of interfaces, increasing cost and complexity. New solutions are integrated from sensor to interface on modern SaaS-platforms with secure communication from smart terminals to the cloud. Low cost, extremely accurate and agile, these systems are up and running in hours. Globally.
In this modern model, teams working on preventive maintenance can also operate as a virtual team. Distence has partners that are delivering services for several remote monitoring hubs that are independent yet can share resources as well as responsibilities.
What can traditional industries learn from this? For one, remote monitoring equals global monitoring if made free from time and place. Second, the monitoring process and the efficiency and productivity of knowledge intensive jobs can be taken to radically new levels. And three, in challenging times, like the ones we are now living, unnecessary physical on-site presence or travelling and new operational models are valuable.
What do you think? – should this remote working be a norm in condition management profession also. Please reach out to us to discuss.